Most often, that wasted time is from trying to use low quality tools for any job. In this case we are discussing screen frames.
Tips from our Print Master installer
Screen frames have more influence on how well and how profitable job are produced. Yes, we are sure you have heard all the hype and looked at all the articles. Yes, we know that screen frames seem expensive and they appear to last forever. Yes, we know you can print through anything. Been there, done that.
However. The real expense is hidden.

Once, a frames has warped, the movement of the mesh is inconsistent from when the screen is exposed to when the when the squeegee presses the mesh to the product. This makes the set up time on press longer. Hence, a time waste for your press operator.
Rigid aluminum frames are dimensionally more stable than wooden frames. They also have their issues. They are more expensive as an initial investment. However, they are also considered equipment and can be depreciated. Wood frames are considered consumable.

Aluminum frames do not absorb ink or cleaning solvents. These items stay on the surface of the frame. The aluminum frame needs to be wiped down after each use to keep the press operator's hands clean.
Both of these frame styles have one HUGE issue that needs to be addressed on a regular basis in every shop. Mesh tension. Yes, we went there. We are not talking about high newton measurement but we are saying that if you can see a job have on the mesh from 5 years ago, chances are the mesh tension is too low. Well, non-existent. This causes problems with registration because of mesh shifting during the print. The image is exposed onto the mesh when there is no pressure against it. However, in order to get ink to clear, you have to apply high level squeegee pressure. How can a job register when it has been stretched out of position?

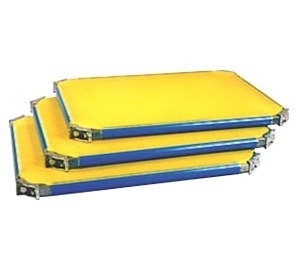
Being profitable and producing high quality work takes some investment.
We try to have our assembly staff use good tools when they build equipment. They move faster and get better results when the tools are high quality. Our installers each have a brand of tools they prefer but they are very picky about which ones are in their bags. And everyone knows that cutting a tomato with a dull knife is a mess. So our suggestion to you is to take a look at what is in your shop. A small investment could save you time, which is the best way to save money.